I had to look at RFID/Barcode options for Maximo mobility solution recently. Although these technologies have been around for decades and have become a commodity, when integrating with other systems like Maximo Anywhere or Everyplace, there are certain problems that we have to deal with. In this post, I’ll discuss a few concerns related to this topic, hopefully, it helps Maximo consultants to save some time when considering the solution. These are just a brain dump of different things related to the topic that I have in mind. Thus, you can read them in any order or only look at the part that you are most interested in.
Barcode vs QR code
When it comes to barcode reading, many people think that they can simply use the built-in camera of the phone or tablet to read barcodes, as seen in many product-comparing apps. However, in an industrial setting, one should consider various extreme conditions that field workers have to work in. For example, in Construction or in Oil & Gas, working at night is common. In such cases, the camera doesn’t do well in reading barcodes. In some of our tests, under pretty good ambient light, reading barcodes takes up to 3-5 seconds while QR code reads almost instantly. In poorer conditions though, the camera simply can’t focus and can’t read anything. Thus, if the requirement is to work in an environment where lighting conditions are always ideal, Barcode or QR codes don’t matter, I’m a bit leaning toward QR code as it read faster and enable higher workflow efficiency. Otherwise, we should consider other options such as RFID or using a laser barcode reader.
Barcode vs RFID
When it comes to barcode (QR code is included in this category) versus RFID, they have very different attributes that one should think carefully before deciding which one suits their requirements the most. Many of the better features of RFID do not apply in certain asset management applications. For example, RFID tags don’t need line of sight to be read or RFID can be read in bulk simultaneously. However, in asset identification, these are usually not required.
However, one feature of RFID that is a clear advantage when compared to Barcode is that RFID tags can be a lot more durable under extreme conditions such as in processing plants where conditions usually involve high-temperature, high-moisture, and can be tampered with chemical/oil, even the some of best weather-resistant barcode label brands can wear out/fade out pretty quick (in few months). In this case, RFID tag is a clear winner.
On the other hand, if working under extreme conditions is not a requirement, I would generally suggest using Barcode as it is much cheaper and simpler to use. For example, we can encode Asset Number or Inventory Item Number directly to print out barcode labels, and on Maximo apps, we will just scan and lookup barcodes using the standard “assetnum” and “itemnum” fields.
If RFID is to be used, we generally need a separate custom field to store the tag’s ID string. Then we have to customize the app to look up asset/item using this field instead of the standard asset/item number. We also need an extra step of reading and updating the tag’s ID string into the record in Maximo before it can be used.
Built-in camera/NFC reader vs specialized reader:
Here I’m discussing the pros and cons of using a built-in camera or NFC reader (NFC is one form of RFID) versus using a specialized, external Barcode/RFID device. A built-in reader is simple and more compact. Thus it is suitable for occasional use.
However, if your application requires frequent reading of barcode/RFID, you should go for a specialized laser barcode reader or RFID reader. These tools are designed specifically for the job, as such, it is a lot more efficient and easier to use. As mentioned above, using the camera to read barcodes under poor ambient light can be problematic, but if a laser reader is utilized, poor ambient light is not a problem as the device has its own laser light source, and can read under any lighting condition.
When it comes to industrial use, investing in specialized tools can be a bit more costly but almost always gives a much better return in terms of improved productivity and user acceptance. One thing to consider with external readers is the field workers usually have to wear/carry many accessories such as PPE equipment, walkie-talkies, harnesses, and other tools. The idea of having to carry an extra phone/tablet and an external reader doesn’t sound convenient. As such, one should consider a higher level of resistance from field workers if an external reader is introduced.
Another drawback if you consider an external Bluetooth scanner is that the pairing-up process between Bluetooth devices and smartphones sometimes isn’t straightforward. These kinds of glitches can sometimes create additional reasons for the workers who resisted change to push back and refuse to use the solution. As such, if possible, choose devices with built-in or connected laser barcode/RFID reader over wireless devices
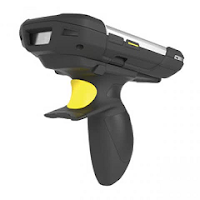
iOS vs Android
Almost everyone prefers using an iPhone or iPad over Android devices. However, the iPhone and iPad are designed for the consumer market. When it comes to industrial use, iOS devices have many shortcomings such as:
- They are not designed to work under extreme conditions such as rain, harsh sunlight
- Insensitivity to touch gestures when workers wear thick gloves.
- Apple is restrictive in terms of providing API for 3rd party developers, as such, there are less options provided by 3rd party vendors when it comes to industrial applications.
In the Energy and Mining industries, the use of intrinsically-safe/non-explosive (EX) electronic equipment is mandatory. This makes the Android platform the only option as currently, no iOS device on the market can meet this safety requirement.
Over the last few years, many companies introduced various computing devices such as smartphones, tablets, and even laptops meeting this standard. Some of those companies include ECOM, Honeywell, and Motorola. Therefore, if you design a solution for use in Hazardous areas that require intrinsically-safe equipment, forget about iOS.
Online only vs Offline support
Here I’m only talking about Maximo Everyplace versus Maximo Anywhere. From Maximo version 7.6, Everyplace becomes a built-in feature. As such, it doesn’t cost anything to use. The process of producing a simplified app by duplicating an existing Maximo application and then modifying it to fit into a small mobile screen to do a specific task generally takes only a few hours to a few days maximum. The users who are already familiar with Maximo will virtually don’t need any training at all. As such, if the working environment has an available wireless LAN or 3G/4G internet connection (which is pervasive and very cheap now), you should go for this solution, it’s a no-brainer.
However, in certain conditions, if a stable connection is not always available, such as inside a deep tunnel for an Infrastructure company or inside a confined space/basement of a large building. In this case, we need to use Anywhere to support offline/online working mode. However, let’s be realistic here. Do your field workers really need to use Maximo app when going in a confined space? A client who I had a chance to work with recently said they need an offline solution because Everyplace won’t work inside underground tunnels. I went around to check and found out that in most areas inside underground tunnels, the 4G network is fast and stable. Some areas may have poor signals. But with the standard work order process, we generally only need access to the app to check in when starting the work, and to check out after the work is done. In this case, identifying and designating several safe areas where network connection is available to check-in and check out would do the job.
With the widespread of 3G/4G repeaters installed by network companies, you might not realise that the 3G/4G network is now available in many areas where it was not possible before like inside tunnels, underground train stations, or parking basements of big buildings.
For other applications such as asset audit/inspection, where users need to use the app to scan the equipment or check-point, if the network connection is unstable, an offline solution will be required.
Maximo Anywhere is a great offline solution because it provides a very smooth experience when transitioning between online/offline working modes. However, it comes with a price. It is very expensive in terms of license fees. It is also a complex platform that requires MobileFirst development skills to configure/customize. Keep in mind that this is still a relatively new solution and not widely proven in the industry, especially when it comes to integration with other 3rd party hardware/software. However, IBM team have been moving really fast with the development of this solution. In the past few years, the solution has seen considerable improvement and level of adoption by the asset management community. So kudos to IBM R&D team for this progress.Considering the significant cost of Anywhere products, we should carefully survey the work environment and take these aspects into account when considering the two solutions.
IBM Mobility vs 3rd Party Solutions
When it comes to mobility solutions for Maximo, most people immediately think of IBM’s mobility solutions which include Maximo Mobile Suites (gone), Maximo Everyplace, and Maximo Anywhere. However, to make an objective evaluation, one must go further than that to evaluate 3rd party mobility solutions such as EzMaxMobile, Datasplice, Syclo Work Manager (now SAP), and many other lesser-known custom-built systems. (eLogBook mobile is one of such solutions which I and my team built when working for Avenue Business Solutions).
The advantage of IBM mobile solutions is that they are open. Therefore, any Maximo consultant with the right skill can customize the apps without IBM’s restriction as long as the users have the right license (which can be very expensive). The problem with IBM solutions is that they don’t always work in practice (e.g. the notorious Maximo Mobile Suites), too complex (Anywhere/MobileFirst solutions), having limited support from IBM (tickets generally take months to resolve or not resolved at all), or having limited material available for developers to customize/integrate.
Gartner over the last several years has been putting IBM mobility solutions under the “Cautions” section. Only in the recent 2017 report did they say something a bit more positive about it which reflects recent developments in IBM Mobile First strategy and the Anywhere solution.
Third-party vendors on the other hand usually have consultants available to come in and guide clients to design processes and implement their products properly and with much lower cost. They are usually smaller companies with dedicated people working in the mobility space, as such they can provide a much better-integrated solution with proven integration modules, software, hardware options and best practice recommendations for processes.
Mobile apps provided by 3rd party companies can be less customizable than IBM’s product, and clients usually have to rely directly on the vendor to provide support, but they are usually very well designed to achieve high efficiency and smooth user experience. Overall, implementing these solutions is usually much more cost-effective, provides better ROI, and clients usually see a much higher success rate.
Hi Viet,
I am a little lost with what way to go, as it stands reading the above I would be going RFID and using android, but what are the requirements for us to start barcoding and implementing the data into Maximo ?
Eg we want to barcode out spares inventory sitting in the warehouse so the crew can manage repairs quickly and with efficiency. However these items will return to the field for 5-10years of work ..
Would you have any extra tips on how to start the process on this end?
We had been using Zebra TC70 android devices with integrated laser scanning, along with Maximo Mobile. However when we went to Maximo Anywhere we were told that the integrated laser scanner is NO LONGER supported (!?!?). We have to buy some sort of additional handheld bluetooth device, which seems to ruin the whole user experience since they now have a device in both hands (?!)
Just got a chance to play around with a TC75 yesterday. Barcode scanning works very well. What is the issue did you have using the TC70 with Anywhere?
Hi!
I've encounter the same issue.
Looking at the official documentation form IBM you have this:
"Bar codes are supported with Blue-tooth enabled external scanner and device camera. If the device has an in-built bar code scanner – then it is not supported."
https://www.ibm.com/developerworks/community/wikis/home?lang=en#!/wiki/02db2a84-fc66-4667-b760-54e495526ec1/page/908583dc-5197-4a3c-ae74-ddbd4bb5437c/version/01890c8c-c7c5-4814-8683-9cd513d044e8
I've also encountered customers that have made configurations to be able to use the "in-built scanners" with the anywhere application.
I'm trying to wrap my head around why the application can't handle the data scanned through the device itself… Any input here around how it works and why it could work with some devices and not others would be greatly appreciated.
I don't have extensive experience with Anywhere. Only a bit of experience with 7.6.1 and 7.6.2 version and don't know what changed in the new one. However, AFAIK, on a Zebra TC7x device, the built-in barcode scanner works like a dump hardware, you push the button, it read the barcode and write the ID string on the field being in focus. So shouldn't need any integration there. Anyway, like I said, I don't know 7.6.3, but I heard from many people that it doesn't work really well. The recent Gartner report seems to confirm that as well. I currently work exclusively with EzMaxMobile only, and it works pretty well.
Thank you for replying!
It's kind of a bad spot for Anywhere as a product, as many companies are using a device with a in-built scanner which simply is not working on many cases. Even got a response confirming certain honeywell devices not working with the laser.
When technicians work in a plant for example, having even more gear to carry is just a dealbreaker seemingly…
Anyway, thanks again!