Maximo Specialist Services and Productivity Tools
Maximo doesn’t work? Maximo is too slow? Maximo is a mess? Too much customisation and no one understands it? I can help you with that
95%
Java customisation removal
120%
Customer satisfaction
200%
Improved performance and efficiency
Services
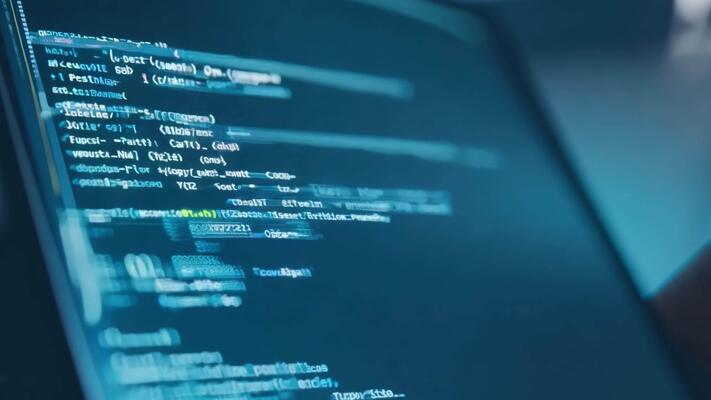
Decustomisation
Too much customisation can slow you down. I have help Australian companies large and small removing and refactoring thousands and thousands of complex Java classes and automation scripts. Once the process is done, your Maximo will be simple, lean, mean and fast.
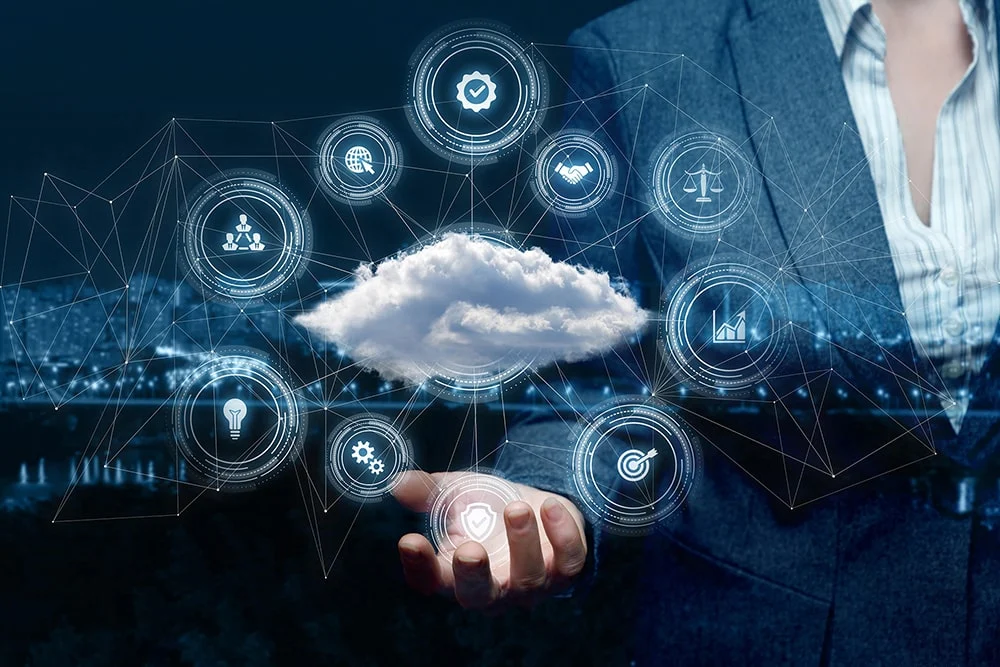
ERP Integration
Need to synchronise PO, Receipt, and Invoice with ERP? Past effort has failed or does not deliver a satisfactory result? I have done a few dozen ERP integration projects with large and small ERP suites. I can help you with this.
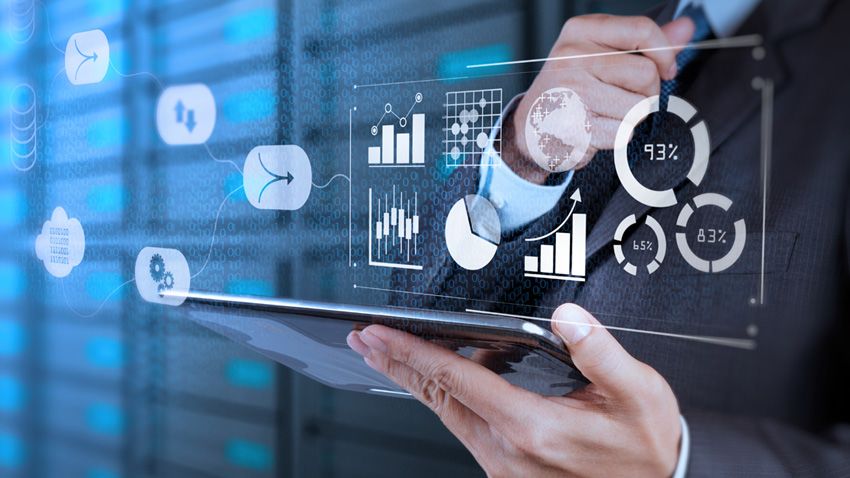
Process Optimisation
End-users complain about system performance? process too clunky? burried in support calls? Those are the symptoms of a system that need optimisation. I have vast experience reviewing Maximo system and processes as a whole to advise on simplifying the system and streamlining the process.
Products
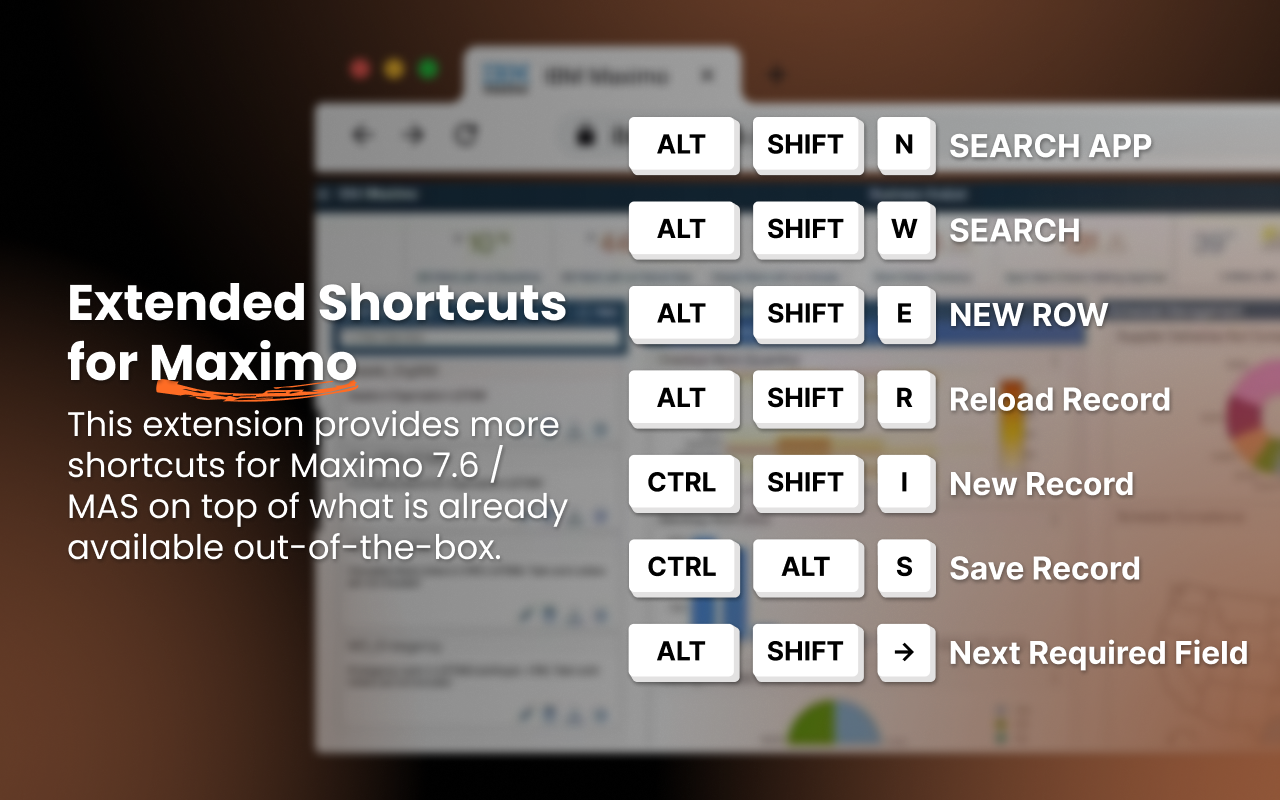
MaxShortcuts
A Chrome extension that provides additional keyboard shortcuts for maximising the speed of navigating Maximo
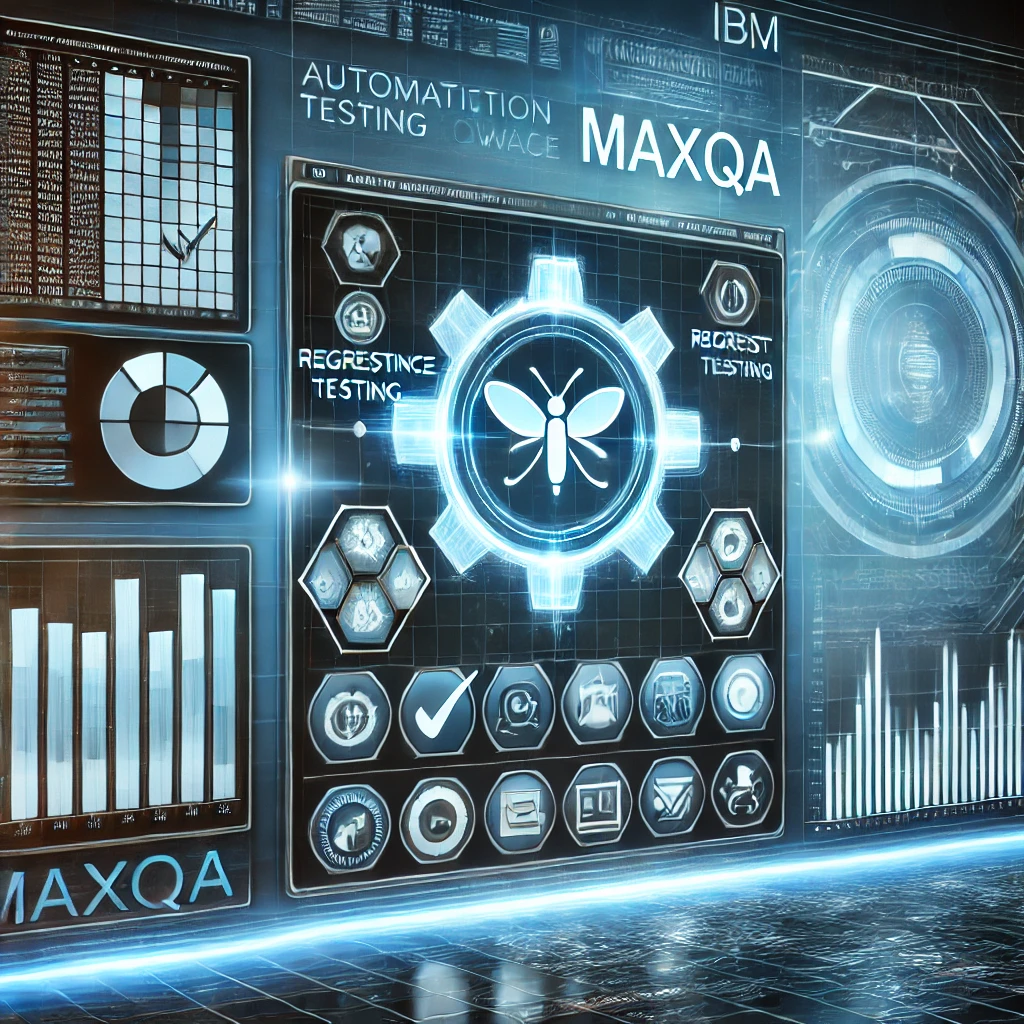
MaxQA
An automation tool which allows the business analyst to build automated test cases in Excel. Works with Maximo and any other web-based application
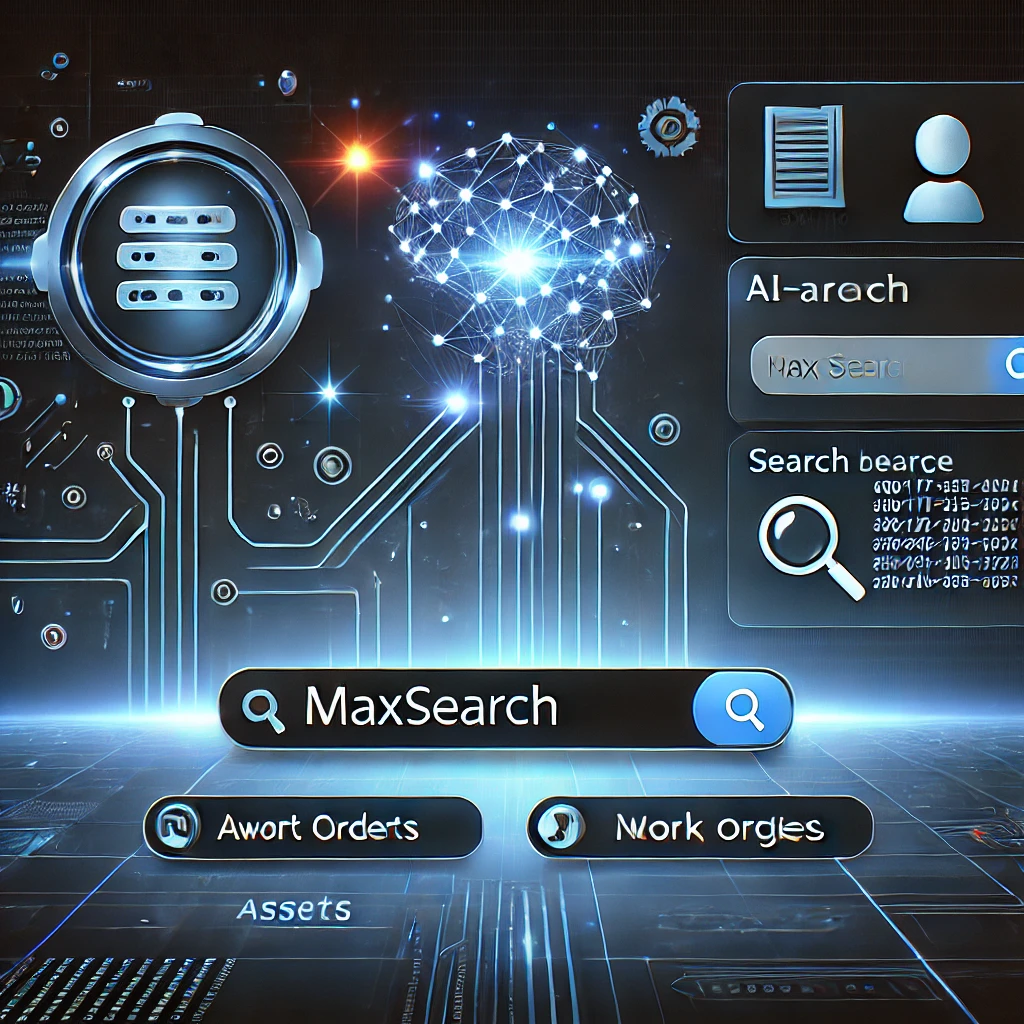
MaxSearch
Index unstructured data such as attachments and images and allow the user to conduct a semantic search of relevant records such as work orders or assets by using natural language
About Me
I am a freelance Maximo consultant with deep unstanding of the software and have track records of delivering measurable results to clients in the Utility, Energy, and Transportation industries.
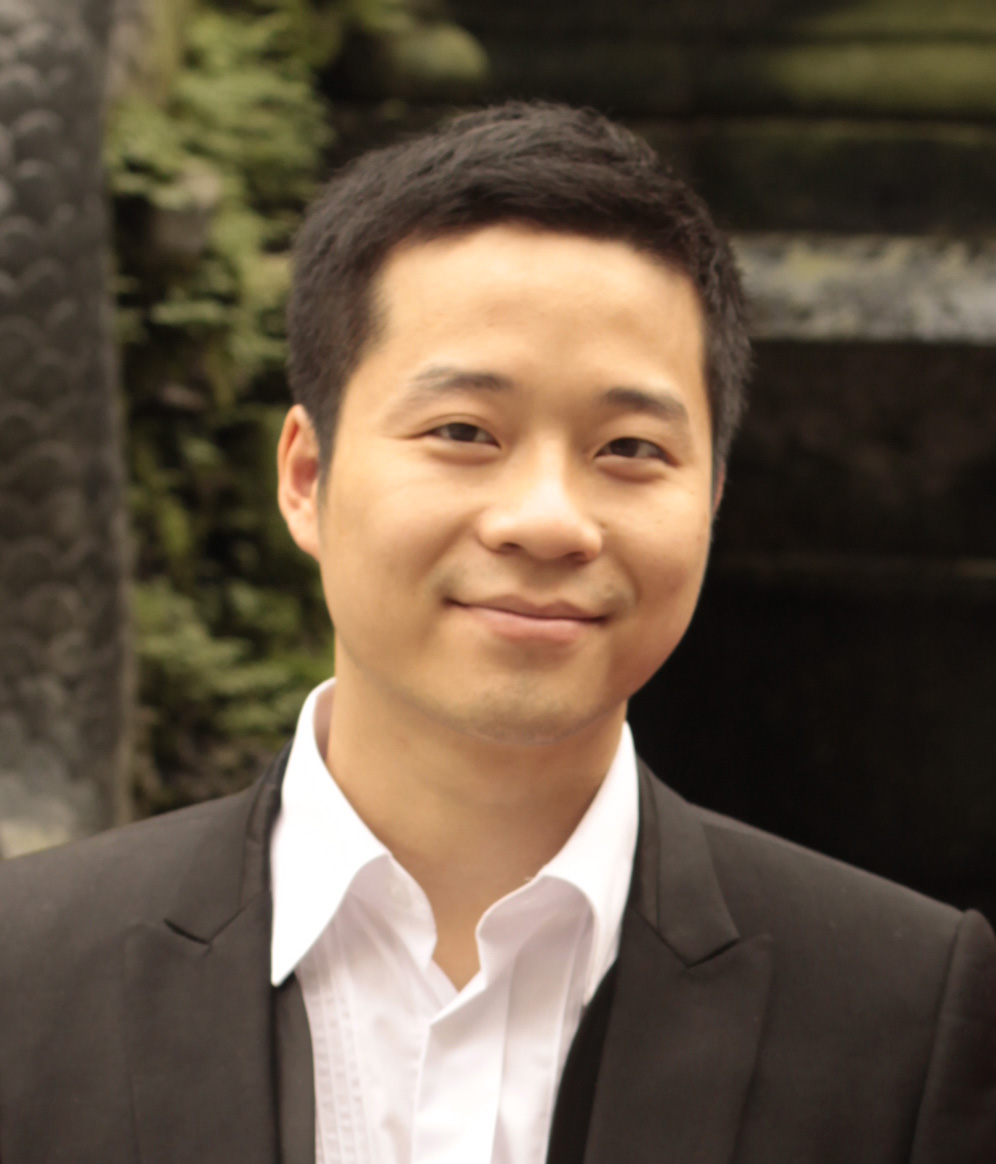
“Viet is the best Maximo consultant I have worked with over my career as an Asset Manager. I’m exceedlingly satisfied with his services. Highly recommend.”

John McAllister
Asset Manager
Want to talk?
If you have a Maximo problem or have an idea and want to see it rolled out in production, we are here to help.